Specialist in rolling
The narrowest thickness tolerances and tensile strength levels particularly deep-drawable grades with the most uniform processing properties, stress-relieved annealed strip, special surfaces, strip for applications requiring extremely high corrosion or temperature resistance – building on more than 200 years of experience as a cold roller, BWS develops individual solutions together with its customers.
Tightest tensile strength levels
Tightest possible tensile strength tolerances
Especially in the production of technical springs, the tensile strength set in the rolling and annealing process plays a decisive role. If it is too low, the spring force is insufficient; if it is too high, the deformation capacity of the material decreases and the parts may break.
The tensile strength describes the mechanical resistance that a material opposes to deformation or separation. As standard, BWS confirms tensile strengths for its own rolled spring steel and precision strips in spans of 150 MPa. Closer spans of e.g. 50 MPa can also be set according to customer requests.
A limitation of the tensile strength compared to the tensile strength levels presented in the standard
is also possible for BWS precision strip customers. Exact adjustment of the required grain size optimizes the processability of the strip for the deep drawing process.
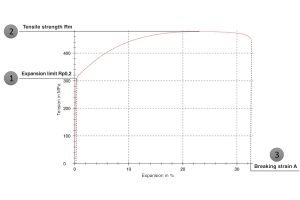
Narrow tolerances
Tolerance over the entire strip length
BWS produces strip with the tightest thickness tolerances over the entire strip length and width. Integrated laser measurement and flatness controls as well as stretching and skin-passing capabilities realize exceptionally good flatness properties.
As standard, BWS confirms at least the product-specific shape tolerances, in each case down to the narrowest tolerance fields (precision tolerance – P) for spring steel and precision strip. Tighter thickness tolerances [e.g. 1/2 P (and tighter)], depending on thickness and width, are of course possible on request.
Shape tolerances
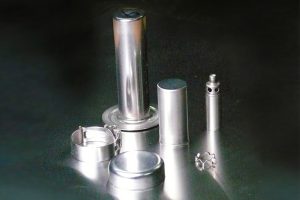
Particularly deep-drawable grades
Evenly processing properties
During the deep-drawing process at the customer’s plant, so-called ears can occur at the edges of the finished parts, leading to scrap or rework. Through an additional rolling step in combination with a special annealing process, BWS can assure its precision strip customers of less than 1% earing.
Deep drawing is a forming process for the production of parts with demanding geometries. In addition to defined mechanical properties, uniform thickness and flatness of the material play a decisive role in the deep drawing process. In order to optimally support particularly demanding deep drawing processes at the customer, BWS offers precision strip as CAF strip, low ear strip or CAF strip in low ear design.
BWS CAF-strip has an extremely homogeneous microstructure. As a result, the material flow during deformation is direction-independent (isotropic). This allows the material to be deformed beyond the theoretical deformation limits.
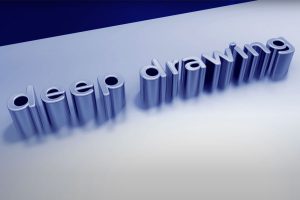
Stress Relieved Strip
BWS Stress Relieved Strip (SRS)
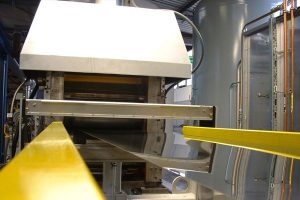
Cold rolling increases the tensile strength of the material. At the same time, the deformation creates an intrinsic stress within the strip that is difficult to detect. If this is released during further processing at the customer’s plant, there is a risk of negative influence on the geometry of the finished parts.
To prevent this, BWS recommends to its customers the use of stress-relief annealed spring steel (SRS) when high demands are placed on dimensional stability and spring behaviour, for example in further processing by etching, the production of healds or fine blanked parts for the electrical industry.
A special thermal process is used to almost completely relieve the residual stress of the strip, thus ensuring the dimensional stability of parts. BWS Stress Relieved Strip (SRS) is available for all materials except titanium.
Surface finish and type of finish
The surface finish and type of finish have a decisive influence on strip properties, such as corrosion resistance, appearance or formability. In addition to the standard surfaces/finishes (2B, 2R, 2H, LC) defined in the current standards (DIN EN 10088-2, DIN EN 10095, DIN EN 10132), BWS produces strips with special surfaces to support processability at the customer’s site and to further improve material properties, if required.
Surface roughness according to customer specifications (matte rolled).
By using specially machined rolls, the roughness values (Ra value) specified by the customer are set during cold rolling. The surface roughness of stainless steels influences, among other things, the corrosion resistance and formability of a material.
Topocrom surfaces
Matt, textured surface with defined high roughness which improves the deep-drawing properties of the material. During the rolling process of the strip, the hemispherical elevations of the work rolls are impressed into the strip surface. The resulting domes in the strip ensure very good forming and coating properties.
Dual-Surface
Top and bottom sides in different surface finishes, a smooth top side can be combined with a rough bottom side, for example.
Finstrip©
By longitudinally embossing the strips during the rolling process, channel-like depressions are created which increase the surface-to-volume ratio (A/V ratio). Width and depth of the channels can be adjusted according to customer requirements. Finstrip© is a special BWS development, e.g. for use in high-performance heat exchangers.
Rolled surfaces
According to the customer’s requirements, the desired pattern is transferred to the surface of the strip by using patterned rollers.
Additional surface finishes are available on request: For example, degreased steels for coating processes or steels coated with deep-drawing foil. Deep-drawing foil reliably protects the surfaces from scratches and drawing marks during the individual processing steps in the case of extreme forming depths.
Possible surface treatments:
- colored annealed
- (partially) coated, varnished
- degreased, electrolytically degreased, grease-reduced, oil-reduced, bright
- brushed
- ground (80 – 400 grit), Duplo (ground and brushed)
- polished
- foiled (protective foil, thermoforming foil).
Overview surfaces
Delivery Conditions | Surface condition | Remarks | Product | |
2B | cold-rolled | dull finish | Condition used for most steel grades to ensure good corrosion resistance, smoothness and flatness, also usual condition for further processing. Skin pass rolling can be replaced by tension levelling. | ![]() |
heat-treated | ||||
pickled | ||||
slightly skin-passed | ||||
2R | cold-rolled | smooth, bright | Smoother and brigther as 2B, this is usual condition for further processing. | ![]() ![]() |
bright annealed | reflecting | |||
2H | cold-rolled | bright | Cold-rolled to achieve higher tensile strength. | ![]() |
LC | cold-rolled | bright rolled | Usual condition of most high carbon spring steels (not stainless) as well as usual condition for further processing. | ![]() |
annealed | ||||
slightly skin-passed | ||||
CAF | cold-rolled | smooth, bright | Corresponds 2R, but improved Condition for future processin. | ![]() |
bright annealed | reflecting | |||
QT | cold-rolled | grey-blue | Condition of hardend high carbon spring steel strip (not stainless) as well as usual condition for further processin. | ![]() |
annealed | polished | |||
colour tempered | ||||
- | cold-rolled dull finish | with defined Roughness value | Special condition for special applications. | ![]() ![]() |
- | rolled surface | with defined pattern | Special design for special requirements in terms of structure and design. | ![]() ![]() |
High corrosion resistance

BWS offers various material grades in its portfolio that provide excellent resistance in a wide range of corrosive media and environments. For example, grade 1.4529 is suitable for use in flue gas desulfurization machines, while duplex material 1.4462 is recommended for applications in the offshore industry.
Corrosion describes the natural process that damages and can even completely destroy metals through reaction with corrosive agents such as chlorides or seawater.
Extreme temperature resistance
Heat-resistant steels are especially suitable for high-temperature stress, including those in industrial furnace construction. Heat-resistant grades, e.g. 1.4878 or 1.4828, have good mechanical properties and are particularly resistant against hot gases and combustion products, as well as molten salts and metals at temperatures above 500 °C.
BWS also offers heat-resistant nickel-based alloys that provide excellent properties against extreme heat. For example, Alloy 601 (2.4851) is resistant up to 1200°C and is used, among other things, for the production of high-speed gas burners.
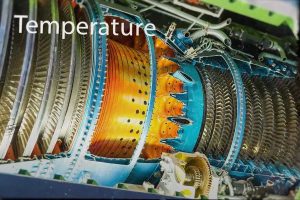