Systems
Complexity and speed determine the day-to-day work of our customers, which BWS strives to flank with the most reliable deadlines and the highest level of quality. BWS is constantly driving forward the further development of its systems, which are the benchmark in the industry, in order to guarantee the high number of orders in customized execution across numerous stages of the value chain.
Logistics concept
By integrating our customers’ supply chain, we achieve the strength of the ServiceMill©, because the combination between the rolling mill and service enables a customer focus that is unique in the industry. While production in the BWS cold rolling mill focuses on combining individual orders into larger production batches with the goal of producing uniform material (e.g. thickness, strength, grain size, etc.), the BWS ServiceCenter focuses on separating the manufactured strip according to the individual customer order (e.g. slitting into different widths with subsequent edge trimming).
In order to master the high complexity of the central value-added processes, the ERP system at BWS is optimally tailored to these complex requirements resulting from the combination of Cold Rolling Mill and ServiceCenter.
For the customer, this means short throughput times and a very high degree of deadline reliability, which also guarantees that special requests can be fulfilled quickly and flexibly.
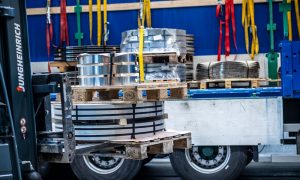
Realiable on-time delivery
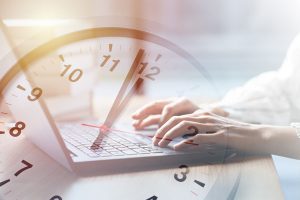
BWS delivers quickly and reliably. This means the ability to deliver at short notice, even for technically demanding products from customer-specific production in the BWS Cold Rolling Mill.
A wide variety of articles in stock guarantees maximum flexibility. The combination of the Cold Rolling Mill and the logistically fully integrated ServiceCenter as the BWS ServiceMill© forms the basis for exceptionally reliable on-time delivery. The interlocking systems of the Cold Rolling Mill and ServiceCenter enable customer-oriented planning and production with short, transparent lead times. When it comes to meeting deadlines, BWS strives to set benchmarks for all industries.
BWS offers standard delivery times of between a few hours (eXpress strip), one to two weeks in service for existing stock material and up to four weeks for customer-specific rolled orders. Order sizes of less than 500 kg are also possible.
Schedule concept | Product Group | typical delivery date | typical lot size | Number of articles in the standard delivery programm | Appointment filling Level |
eXpress | Spring/Precision Strip | 24 h - 1 week | < 500 kg | > 1,400 | > 99 % |
Service | Spring/Precision Strip | 1 - 2 weeks | 250 - 10,000 kg | > 350 | > 95 % |
RollingMill | Spring/Precision Strip | < 4 weeks | > 2,000 kg | > 750 | > 90 % |
Quality Management
BWS uses quality management as an opportunity for market-oriented further development. The goal of customized systems is to manufacture BWS products in defined, reliably achievable quality within minimum tolerance limits. All employees pull together to realize a flexible adaptation to customer requirements while ensuring a high level of quality with high adherence to schedules and competitive costs.
Each coil is tracked from goods receipt to outgoing goods in customer-specific coil specification, which means it can be traced back to its origin at any time across all production and value chains. In this way, in the event of possible production failures, the cause of the defect can be eliminated and other, possibly defective material can be clearly identified.
In its own testing laboratory, BWS carries out chemical and metallographic tests and examinations of tensile strength, yield strength, elongation at break, bending and hardness properties, among others. Individual work certificates (2.2) and acceptance test certificates (3.1) in accordance with DIN EN 10204 can be issued on request.
Continuous quality assurance and constant improvement ensure that products and associated processes are manufactured with consistently high, reliably achievable quality.
As a competent partner, even for the most demanding customers, including those in the automotive industry, BWS is continuously working on the further development of its systems. We are certified according to DIN EN ISO 9001, IATF 16949 and AD 2000 W0. New requirements imposed by the standard are constantly incorporated into the workflows and processes at BWS.